How Evlon® Film is Made

- Plants are grown in the earth and picked by farmers.
- At the mill the plants are cooked 30 to 40 hours at 50°C.
- The machines grind the plant to extract the starch.
- A micro organic process ferments the plant creating lactic acid.
- Lactic acid is heated creating lactide monomers.
- Lactide molecules are opened then linked into polylactide polymer.
- The resulting natural plastic is formed into PLA pellets.
- Bi-Ax converts pellets into crystal clear high grade Evlon film.
- Rolls of Evlon film are made into packages.
- Packaged film is put into composts where it converts to mostly water and CO² within 90 days.
Quite simply...
NatureWorks® and Total Corbion bio-polymer produce the polylactide resins used to make Evlon Compostable Plastic Film. Through a series of fermentation and extraction processes, plant-based sugar molecules are transformed into lactide monomers and then ultimately, into bio-polymer pellets. The pellets are then converted into Evlon Compostable film by BI-AX International.
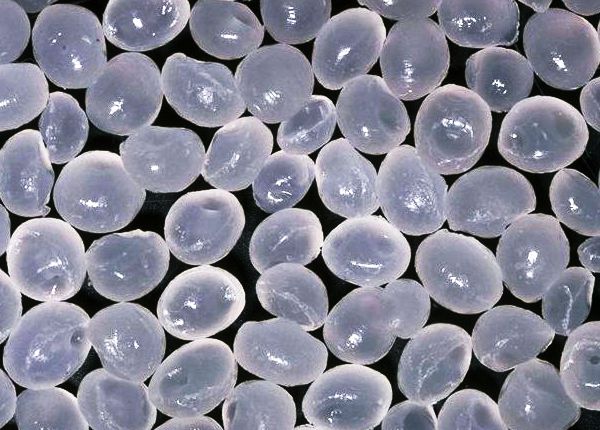
Polylactide is simply a polymer chain made up of lactide monomers.) Visit NatureWorks® for complete information about NatureWorks® bio-polymer or Total Corbion for their product information. Bio-polymers can now be sourced from non-GMO feedstock if required.